How Madevo Improved Operational Efficiency in the Gas Industry.
At Madevo, we are passionate about exploring how AI can revolutionize the gas industry. Here is an exemplary scenario to showcase what our AI assistant can do. For anonymity purposes, we will call this company X.
Introduction:
X, a leading natural gas provider in the UK, faced mounting challenges in optimizing its vast infrastructure. Aging infrastructure, challenging data collection techniques, and a lack of real-time insights were impeding their ability to detect and resolve operational issues quickly. This led to higher expenses, safety issues, and a decrease in consumer satisfaction.
The Problem:
X relied heavily on manual data collection methods, where employees physically visited sites to record pressure readings, leak detections, and meter readings. This time-consuming approach was prone to human error and provided little insight into the overall health of their infrastructure.
Furthermore, its outdated infrastructure could not relay real-time data, making it harder to fix problems and minimize interruptions. Aging pipelines and equipment were suffering from corrosion, leading to leaks and increased maintenance costs
Misallocation of gas resources was leading to supply shortages and excess inventory. It was a challenge to deliver gas to the right locations at the right time.
The Madevo Solution:
X partnered with Madevo, to implement a comprehensive data-driven solution. Madevo worked with existing advanced sensors across Xs distribution infrastructure, including:
- Pressure sensors: Continuously monitored gas pressure levels throughout the pipelines, allowing for early detection of leaks and pressure fluctuations.
- Temperature sensors: Monitor ambient temperature to assess the impact on gas properties and equipment performance.
- Flow meters: Tracked gas flow rates in real-time, enabling X to optimize gas delivery and identify potential inefficiencies.
- Toxic gas sensors: Monitor for toxic gases, such as carbon monoxide or hydrogen sulfide, to ensure safety and compliance with regulations.
- Humidity sensors: Measure humidity levels, which can affect gas volume and pipeline integrity.
- Smart meters: Provided granular data on individual customer consumption patterns, facilitating targeted billing and improved customer service.
- Vibration sensors: Detect abnormal vibrations in equipment, such as compressors or pumps, indicating potential mechanical issues.
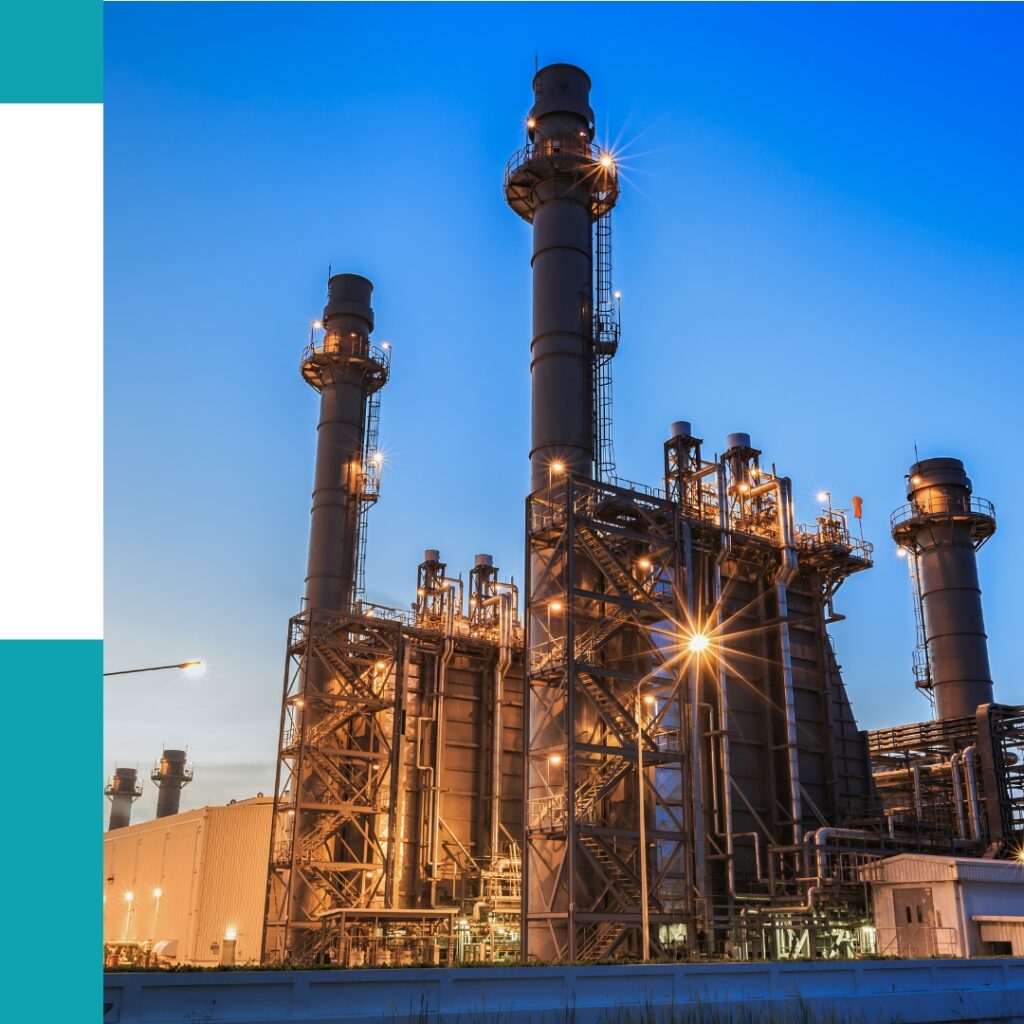
Madevo’s Impact:
Madevo’s AI assistant seamlessly integrates with X’s existing infrastructure, enabling real-time data collection and analysis. This resulted in a multitude of benefits:
- Enhanced Operational Efficiency: Real-time insights from sensor data allowed us to optimize pipeline pressure, reduce gas loss, and schedule maintenance activities proactively. This led to significant cost savings through minimizing wasted resources and reducing downtime.
- Improved Safety: The early leak detection capabilities provided by Madevo’s solution minimized safety hazards associated with gas leaks. X could now identify and address potential issues before they escalated into major incidents.
- Empowered Employees: Madevo’s user-friendly interface provided X’s employees with easy access to real-time data and actionable insights. Field technicians could now make informed decisions on-site, improving their efficiency and effectiveness.
- Data-Driven Decision Making: X gained valuable insights into its infrastructure performance, enabling them to make data-driven decisions for infrastructure upgrades, resource allocation, and overall infrastructure optimization.
- Enhanced Customer Satisfaction: Real-time data on individual customer consumption patterns allowed X to offer personalized billing solutions and identify potential service issues proactively. This resulted in improved customer satisfaction and loyalty.
- Reduced Environmental Impact: By optimizing gas distribution and reducing leaks, Madevo helped minimize their environmental footprint and contribute to a more sustainable future.
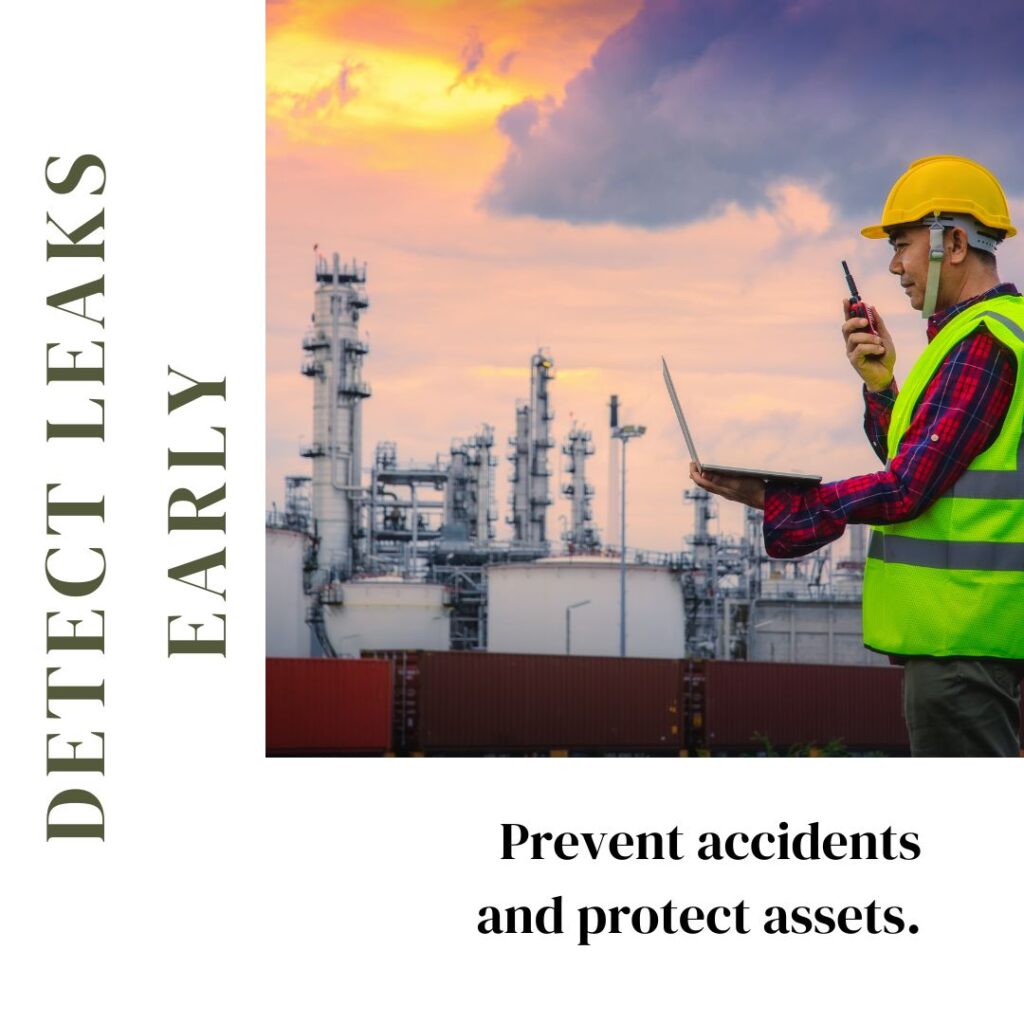
Beyond the Basics:
Madevo offered the potential for further advancements:
- Predictive Maintenance: By analyzing historical sensor data and identifying trends, Madevo helps X predict equipment failures and schedule maintenance activities before breakdowns occur, minimizing downtime and associated costs.
- Advanced Analytics: Madevo’s platform provided the foundation for leveraging advanced analytics tools to gain deeper insights into infrastructure performance. This helps X identify areas for further optimization and develop a more holistic understanding of its gas distribution network.
- Integration with Existing Systems: Madevo’s open architecture allowed for seamless integration with X’s existing enterprise resource planning (ERP) and customer relationship management (CRM) systems, enabling a unified view of their operations and customer data.
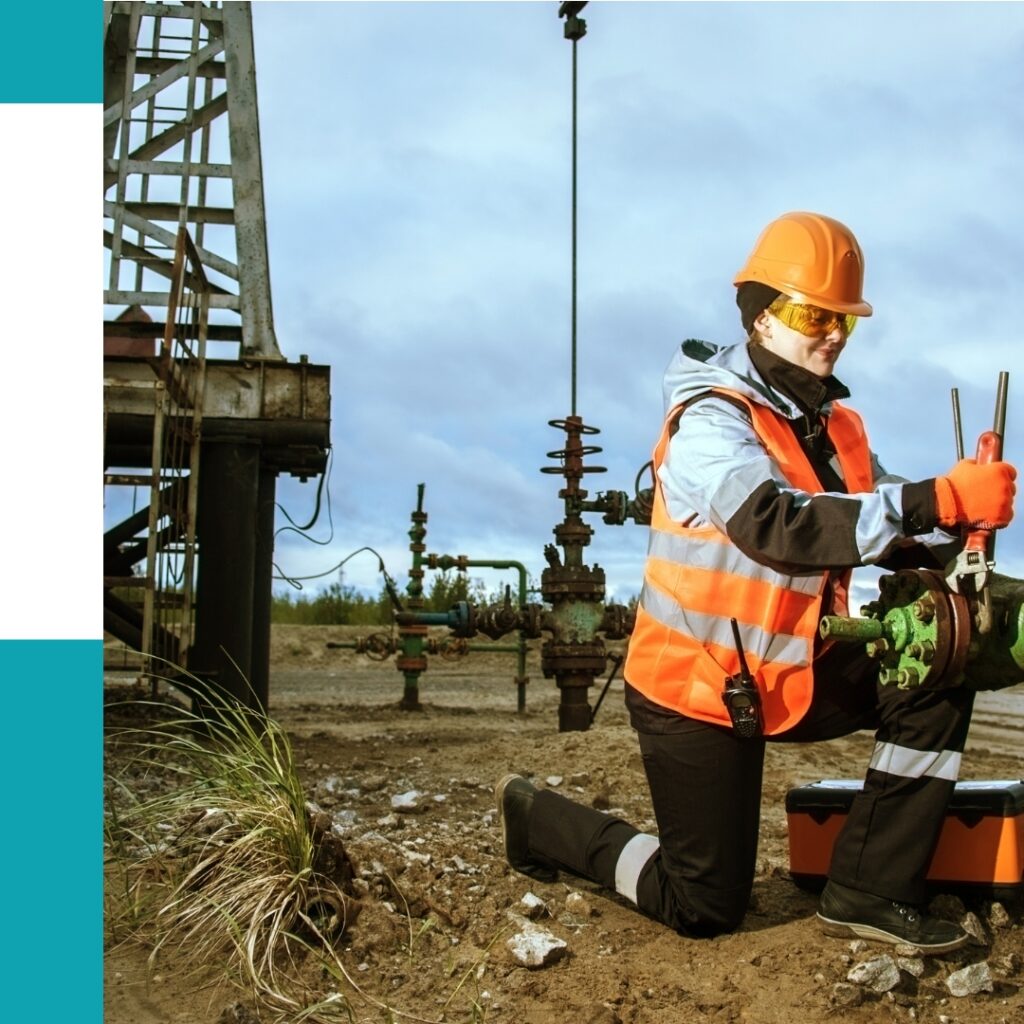
Conclusion:
X’s partnership with Madevo is a testament to the power of AI to transform the gas industry. By leveraging real-time data and actionable insights, X’s achieved significant improvements in operational efficiency, safety, and customer satisfaction. Madevo’s AI assistant provided a scalable and adaptable solution, empowering X to optimize its infrastructure and gain a competitive edge in the market.
Would you like to improve your company’s infrastructure, processes, and connectivity? Let’s talk about it!
Give us a follow on LinkedIn, X, or YouTube to be updated on our news!
Check our video on gas operations: